Case study: Mainmark’s Teretek resin injection technology treats subsidence at Kent School
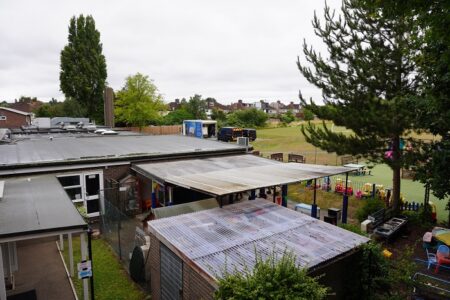
Traditionally, underpinning is used to address subsidence, but this is costly and time consuming
While the RAAC scandal may have been in the news in recent weeks, it is not the only remediation issue that is affecting what has been termed as Britain’s crumbling school estate.
When the nursery building at Dulverton School in the London borough of Bexley in Kent, showed signs of subsidence, the council chose Mainmark’s Teretek resin injection technology, rather than traditional underpinning, to treat the problem.
“I was looking for a solution that would suit the time-sensitive nature of the project and that could achieve the necessary geotechnical engineering improvements with as little disruption to the school as possible,” explains Nicole Burnett, project engineer at Bexley Council.
“I contacted Mainmark to enquire about its resin injection technology and put this forward to be approved.
“I am pleased that the project objectives were achieved and will look to add polymer injection technology as a consideration for future projects.”
Constructed in the 1960s, the nursery building was showing signs of subsidence, with large cracks visible inside the classroom walls and ceiling as well as stepped cracks appearing in the brickwork outside.
A geotechnical survey and other investigations were carried out.
Part of these were trial pits that were dug out to expose and examine the foundations.
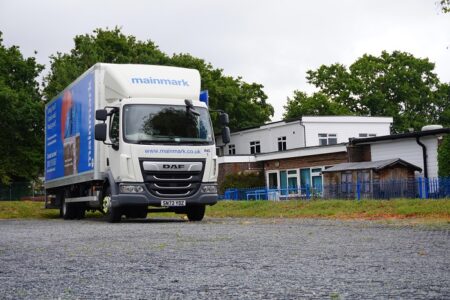
Using Mainmark’s resin injection technology, the project was completed in two days
It was determined that the subsidence was caused by the clay soil beneath the foundations shrinking during the high temperatures of the long dry summer of 2022.
And the situation was exacerbated by nearby trees drawing moisture from the ground.
The geotechnical consultants on the project proposed traditional underpinning as a solution. However, as this would have required extensive excavations as well as causing considerable and lengthy disruption to the school, Burnett decided to explore alternative options.
After seeing the detailed information offered on resin injection technology on Mainmark’s website, she contacted the company to find out more.
A detailed quote and methodology statement for the use of Teretek resin injection technology to treat the subsidence that affected two walls of the school was then sent to the council.
Having confirmed with both her structural engineer and building control manager that this was an accepted remedial solution for subsidence treatment, Burnett specified Teretek as the solution for ground improvement.
Q: How does resin injection technology work
A: Resin injection technology works by delivering a polymer resin into the soil under, or near to, the foundations suffering from subsidence.
For the treatment, 16mm holes are drilled into the ground to reach the soil beneath the foundation or, if required, holes of the same diameter are drilled through the concrete slab within the building.
In some cases, the small diameter boreholes are drilled both inside and outside of the building.
The resin is pumped through injection tubes inserted at predetermined depths by highly-skilled ground technicians using handheld equipment.
For Dulverton school all the geopolymer was injected from outside the building under the full length of the north wall and part of the west wall.
Once the liquid was injected, it quickly expanded and filled any voids, cracks, and fissures in the soil before rapidly setting to form a solid mass of geopolymer resin at required depths, compacting the soil as a result.
Through careful control of the resin mix and volume injected, the load-bearing capacity of the ground beneath the foundations was increased.
Laser monitoring on the outside of the nursery building at Dulverton and visual checks of the inside of the classrooms during the treatment were used to assess progress.
And laser monitoring enabled Mainmark to be able to confirm that they had achieved the 1mm to 3mm lift required at the specific points in the treatment zone.
Post completion, this showed that the ground at depth below the foundations had been sufficiently improved.
Due to the rapid nature of the process and the ease of access to key points on site when using handheld equipment, the subsidence treatment using Teretek took only two working days.
Burnett said: “It seems less intrusive and can be completed much quicker than traditional underpinning”
The treatment was scheduled and completed at the start of the holidays, leaving time for any remedial works to take place at the school with the reassurance that the subsidence issue had already been treated and was backed by Mainmark’s 20-year product warranty.
Due to the non-intrusive nature of the subsidence treatment, and the ability of the geopolymer resin to provide some lift, the remedial work was minimal. This contrasts with traditional underpinning, where the excavation work and heavy machinery required can result in remediation work required both inside and outside the building being treated.
Q: Why is resin injection more suited educational establishments than traditional underpinning?
A: As is the case in all educational establishments, the priority for Dulverton School when faced with subsidence was to rectify the problem quickly and effectively, with minimal disruption to the education of the pupils under its care.
At all times the safety of the staff and pupils is paramount, and the pressure is on to be able to keep the school open and carry out any work required outside of term time.
When looking at the options for treating subsidence, traditional underpinning, with its requirement for equipment for ground excavations, spoil disposal and concreting or underpinning, is a time-consuming and complicated process, with treatment times of around three weeks. It cannot match the minimal disruption and rapid treatment times on offer from resin injection technologies.
The Teretek treatment at Dulverton took only two days to complete and the speed and flexibility of the technique means it can be employed over weekends or during half-term breaks, limiting disruption to schools.
Cost, of course, is also a concern, especially given the limited budgets on which schools are having to operate.
Traditional underpinning, with all the equipment, disruption, and time required to carry out the process is usually a more-expensive option when compared to resin injection technology.
Burnett said: “We obtained quotes for underpinning, but this came in at a much-higher cost and would have been much more intrusive for effectively the same result.”
When looking at the condition of the educational sector as described in a recent National Audit Office (NAO) report it states that 38% of schools have now passed their estimated design life.
And the expectation is that these will eventually require either completely rebuilding or refurbishing. The latter is usually the more-cost-effective choice, however refurbishing can add extra weight to existing foundations.
This is where the ground-strengthening ability of resin injection technology could be used to good effect to provide a stronger base beneath the foundations and mitigate against the risk of future subsidence.
Using Mainmark’s Teretek resin injection technology proved itself to be a cost-effective solution for Bexley Council when looking to treat subsidence at Dulverton school.